거대한 강철로 이루어진 공장 안에서 클래식 음악과도 같은 경쾌한 멜로디가 울렸다.
17일 오후 1시께 르노코리아자동차의 미디어 팸투어 프로그램으로 부산시 강서구 신호산업단지에 있는 부산공장을 찾았다. 1997년 완공된 르노코리아자동차의 생산기지이자 세계 수출 1번지인 부산공장에서는 차체 조립부터 엔진 공정에서 발생하는 무거운 소음을 뚫고 또 다른 기계음이 들렸다.
이 소리의 정체는 공장 곳곳을 돌아다니는 무인 운반 시스템(AGV)이다. 고효율 스마트 공장을 추구하는 르노코리아는 220여 대의 AGV를 활용하고 전 공정에 약 95% 이상의 자동화를 이뤄냈다. 작업자의 동선을 최소화하면서도 작업능률을 높이기 위함이다.
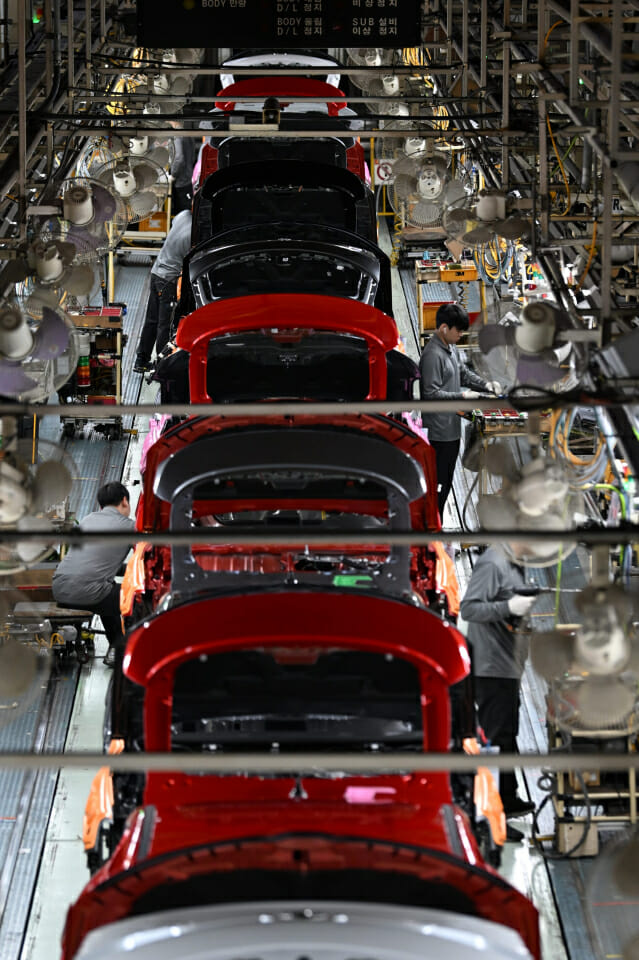
실제로 이날 방문한 엔진공장에서는 오후 1시 31분 기준 시간당 85대 계획에 실적은 89대로 3대에서 4대 이상 효율적으로 차이를 벌렸다. 르노코리아의 엔진공장은 173명이 근무하며 1년에 18만대를 생산할 수 있다. ‘고효율과 유연성’을 강조한 르노 부산공장의 슬로건답게 작업자들은 최소한의 동선으로 최대의 작업량을 뽐냈다.
르노코리아는 하이브리드 차량에 탑재되는 배터리도 자체 제작하고 있다. 엔진공장 한편에 마련된 배터리 공장은 화재 위험성까지 철저하게 대비하고 있다. 이곳에서는 연간 10만대의 배터리를 생산할 수 있다고 르노코리아 관계자는 설명했다. 화재 발생 시에도 공정 시설은 최대 1시간, 창고는 최대 2시간을 막을 수 있게 설계됐다고 덧붙였다.
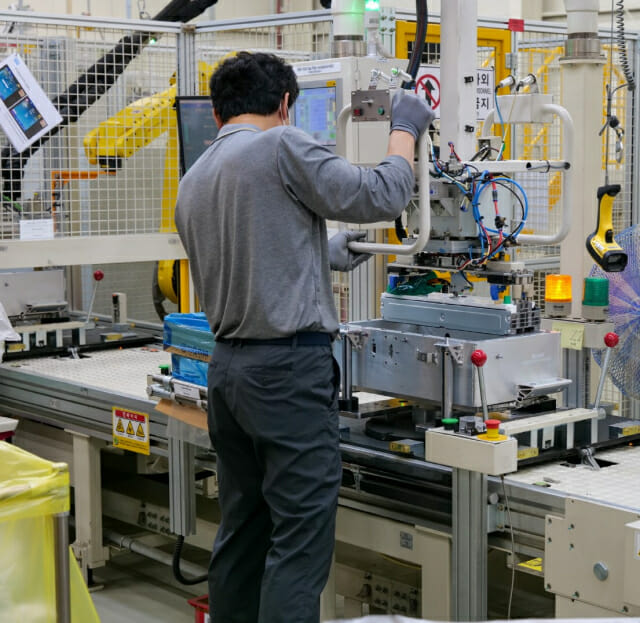
르노코리아 부산공장에서 제작되는 엔진은 해외 시장에서도 인정받고 있다. 국내 공장에서 생산돼 글로벌 출시되는 차량에 탑재되는 경우가 더러 있다는 것이다. 이곳에서 제작되는 ‘MR18DDt’ 고성능 엔진은 르노의 고성능 브랜드 알핀에 탑재된다. 국내에서 단독 생산되는 엔진이 글로벌 시장에 인정받은 것이다.
장소를 옮겨 최근 수출 선복난에 직면한 자동차 업계의 대안을 성공적으로 제시한 르노코리아는 컨테이너 선적이 어떻게 이뤄지는지 보여줬다.
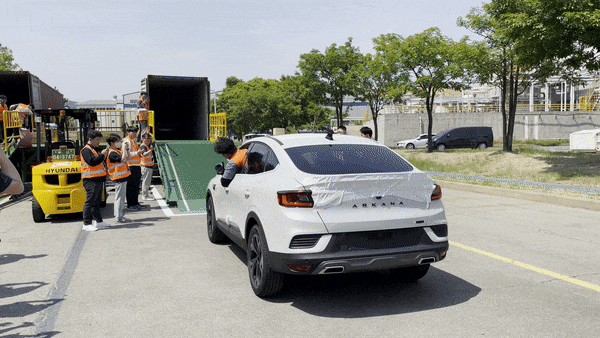
르노코리아에 따르면 현재 컨테이너 수출은 XM3(르노 아르카나)만 진행된다. 한 컨테이너당 3대씩 적재되며 현재 전체 수출 물량의 10%를 프랑스로 보내고 있다. 르노코리아 측은 하반기부터는 영국과 이탈리아 등 추후 다른 국가까지 확장할 계획이라고 설명했다.
컨테이너 선적은 하루에 최대 25대다. 시간은 약 20분 정도 걸리는데, 일반 선적보다 10% 저렴하다는 장점이 있다. 무엇보다 수출선에 따라 일정에 영향을 끼치는 부분이 정기선을 이용하면 비교적 무리 없이 효율적으로 스케쥴을 관리할 수 있다는 강점도 존재한다.
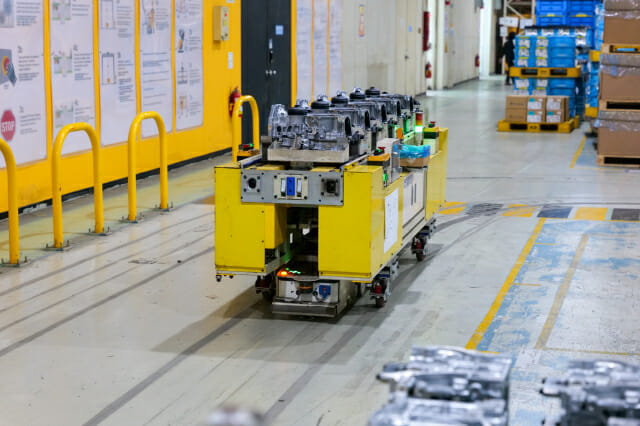
르노코리아 부산공장은 전반적으로 고효율 작업 환경이 구축되어 있다는 느낌을 줬다. 업계 관계자는 “르노그룹의 전통적인 엔지니어로서 근무해 왔던 스테판 드블레즈 사장은 프랑스 사람답게 효율적인 방법을 추구하고 검소하다”고 “한국인도 효율을 강조하기 때문에 이는 시너지 효과”라고 평가했다.
부산공장 내부는 곳곳에 효율을 강조한 면면을 찾아볼 수 있다. 모든 공장 내부에는 라인마다 부품을 쌓아두지 않는다. 바닥에 깔린 검정 선을 따라 AGV가 필요한 부품을 조달해 주기 때문이다. 이와 함께 곳곳에 로봇이 자리해 검수 과정과 일부 사람 손이 거쳐야 하는 부분을 빼고는 대신 작업하고 있다.
이 같은 자동화율은 르노 그룹 내 최고 수준의 생산 품질 유지로 자리할 수 있게 됐다.
르노코리아 관계자는 “부산공장은 르노그룹 내 품질 수위에서 1, 2위를 벗어난 적이 없다”며 “생산성도 5위 내로 유지하고 있다”고 말했다. 이어 “검사 프로세스도 강화해 7개의 검사단계를 통해 최소 300% 이상의 품질 검사를 실시하려고 노력하고 있다”고 덧붙였다.
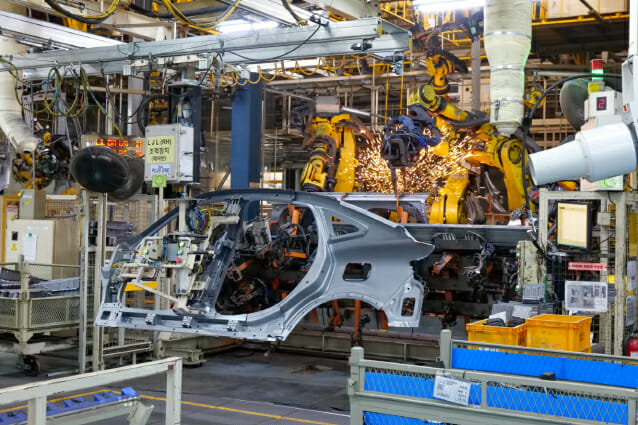
효율과 함께 혼류 생산에도 강력한 공정을 유지하는 유연성도 눈에 띄었다. 르노그룹 내 대부분 공장은 한 라인에서 한 모델만 생산한다. 하지만 르노코리아 부산공장의 조립공장은 3개 차종(XM3, SM6, QM6)을 함께 생산하고 있다. 이는 생산성으로도 직결된다.
혼류 생산의 가장 큰 단점은 다른 차종의 부품이 장착되는 경우다. 부산공장은 이에 대비해 이품장착 방지 보조시스템을 강화했다. AGV를 통해 차종마다 정확한 부품을 제공하게 설계했다. 이외에도 조립시 ▲체결품질보증 시스템 ▲품질추적관리 및 비전 검사보증 시스템 ▲스마트팩토리(디지털 워크스테이션) ▲전기장치 품질보증 시스템을 통해 출고와 인도 전 검사를 끝마친다.
이중 스마트팩토리는 각 검증 과정마다 태블릿을 설치하고 품질 검사한 부분을 체크한다. 이 품질 정보는 공장 서버로 전송된다. 이를 통해 실시간 품질 피드백과 문제 발생 시 관리자와 작업자간의 협업도 강화했다. 또한 공정 전체에 대한 실시간 라인 체크도 가능하다.
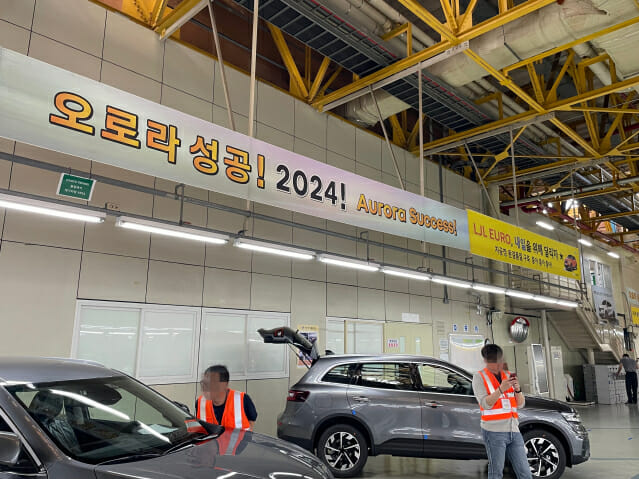
르노코리아는 올해를 한 단계 더 도약하기 위한 '숨 고르기의 한 해'로 삼고 있다. 내년인 2024년에는 르노코리아자동차의 저력이 담긴 라인업 구축에 나서겠다는 전략이다. 이 프로젝트의 명을 ‘오로라’라고 지정하고 공장 내부에 이 같은 의지를 담은 현수막도 배치했다.
관련기사
- 제네시스, 'G70·G70 슈팅브레이크 연식변경' 출시…4315만원부터2023.05.18
- 토요타, '연비왕' 하이랜더 韓출시 초읽기…"펠리세이드 나와!"2023.05.17
- 안전한 車 볼보, 수입차 고질병 고치고 2만대 클럽 '진격'2023.05.16
- 제값받은 현대차그룹…‘양품염가’ 토요타 영업익 넘었다2023.05.16
오로라 프로젝트에는 지리그룹의 스웨덴 연구개발(R&D) 센터에서 개발한 CMA 플랫폼과 차세대 하이브리드 시스템이 적용될 예정이다.
올해 1월부터 4월까지 르노코리아는 비교적 부진한 성적을 냈지만, 다양한 수출 활로를 개선하고 최대한의 공급과 수요를 맞추기 위한 개선을 이어 나가고 있다고 회사 측은 강조했다.