국내 3D프린팅 관련 산업, 학계 전문가들이 국내 3D프린팅 기술의 산업 확대 적용 방안과 이를 위해 풀어야 할 과제를 짚었다. 국내 산업현장에서 제대로 활용되려면 국산 3D프린팅 소프트웨어 개발이 시급하다는 지적이 나왔다.
3D프린터로 뽑아낸 출력물이 다양한 전자적 기능도 수행해 전기차, 사물인터넷(IoT) 등 분야에서 널리 쓰이도록 전자소자와 융합된 기술에도 관심을 가져야 한다는 주장도 따랐다.
유럽, 미국의 선진기업들이 산업용 금속 3D프린팅을 이미 산업 현장에서 활용하는 사례를 참고해 국내 기업들도 선행적으로 기술 도입을 시도해야 한다는 의견도 나왔다.
한국미래기술교육연구원은 20일 서울시 영등포구 소재 전경련회관에서 ‘4차산업을 위한 3D프린팅 최신 개발 이슈와 산업 확대 적용방안’ 세미나를 열었다.
이날 자리에는 국산 3D프린팅 소프트웨어를 개발 중인 전자부품연구원부터 국내 1세대 3D프린터 전문업체 캐리마, 3D프린터를 이용해 제품을 제작, 가공하는 국내 기업 인스텍 등 산학연 전문가들이 모였다.
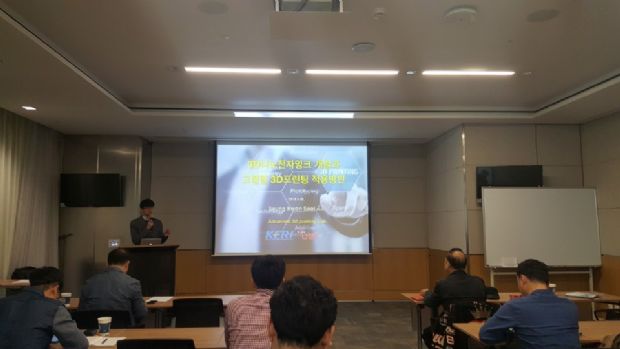
신화선 전자부품연구원 책임연구원은 국내 3D프린팅 기술이 산업 현장에서 쓰이고 해외시장에서 경쟁하려면 국산 소프트웨어가 있어야 한다고 강조했다. 신 책임연구원은 3D프린터가 소재를 한층씩 출력해 결과물을 만들 수 있게 하는 데 필요한 슬라이싱(Slicing) 소프트웨어를 개발 중이다.
신 연구원은 “똑같은 3D프린터 2대에 각각 다른 소프트웨어를 활용해 출력해보니 결과물 품질이 다르게 나왔다. 소프트웨어에 내재된 것(출력물 품질 원인)이 많다”며 “큐라 같은 해외사들이 오픈소스로 소프트웨어를 제공하지만 이는 해외 특정 3D프린터 장비를 고려한 소프트웨어라 국내 장비와 맞지 않다”고 설명했다. 이어 “소프트웨어를 바꿀 수 없으니 결국 장비를 고치면서 모방제품이 나오게 된다. 국산 장비 장점이 날아가는 것”이라고 덧붙였다.
신 연구원은 또 우리나라가 반도체 분야의 형상 모니터링 분야에 세계 최고 기술을 가진 만큼 3D프린팅이 뽑아내는 출력품이 원본과 얼마나 같은지 검사하는 형상 모니터링 시장을 우선 선점해야 한다고 밝혔다.
설승권 한국전기연구원 박사와 양용석 한국전자통신연구원 박사는 전자소자를 융합한 3D프린팅 기술인 3D프린팅 일렉트로닉스 잠재력을 강조하며 국내 3D프린팅 업계 주목을 촉구했다. 두 박사 모두 해당 기술을 연구 중이며 기술이 상용화된다면 전기자동차나 로봇, 의수 등에 적용돼 전자적 기능을 부여할 수 있을 것으로 기대했다.
설 박사는 “현재 3D프린터로 아이언맨 모양 플라스틱 모형은 만들 수 있지만 영화에서처럼 다양한 기능이 탑재되진 못 한다”며 “3D프린팅 출력물에 전기가 통하게 하거나 자성 성질을 넣을 수 있게 되면 센싱 등 전자적 기능을 부여할 수 있다”고 강조했다.
양 박사 역시 “현재 대다수 의수는 아무런 기능도 없지만 매우 고가”라며 “3D프린팅 전자소자를 만들면 다양한 기능이 들어간 의수를 저렴하게 만들 수 있다”고 설명했다.
강민철 3D프린팅연구조합 상임이사는 국내 생산제조 기업들이 장기적 관점에서 3D프린터 장비부터 소프트웨어, 소재 등을 공장에 들여놓고 생산제조 과정에 적용시키는 시도를 해야 한다고 주장했다. 이미 독일, 이탈리아 등 기업들은 3D프린팅 시스템을 두고 필요할 때마다 부품 등을 생산해 바로 보급하는 식으로 업무 효율성을 높인다는 설명이다. 기존 제조 방식으론 생산할 수 없는 복잡한 장치도 3D프린팅은 만들 수 있다는 장점에 주목해야 한다는 의견도 내놨다.
강 이사는 “독일, 이탈리아에선 작은 공장에도 금속 3D프린터가 3개씩은 있을 정도로 엄청 많지만 우리나라는 그렇지 않다”며 “구조가 복잡한 열교환 장치는 전통 방식으론 뽑을 수 없지만 3D프린팅은 가능하다. 앞으로 10~15년 뒤 자동차 산업의 핵심 기술 분야에서 주조, 프레스는 거의 다 사라지고 3D프린팅 기술, 즉 적층 방식이 각광받을 것”이라고 내다봤다.
김진호 KTC 대표와 김대중 인스텍 이사 역시 이미 해외 생산제조 현장에선 산업용 금속 3D프린팅 기술이 많이 활용해 생산 비용을 크게 줄이고 있다고 말했다. BMW그룹, 제너럴일렉트릭, 필립스, 지멘스 등 해외 선도기업들이 직간접적으로 금속 3D프린팅 기술에 투자하는 만큼 국내 기업들도 관심을 가져야 한다고 강조했다.
김 대표는 “해외 주조 산업에선 복잡한 작업 과정과 오랜 작업 기간 등 어려움을 해결하기 위해 3D프린팅 기술을 하이브리드 형식으로 활용하고 있다”며 “정밀 공정에서도 3D프린팅이 잘 쓰이고 있다”고 밝혔다.
김 이사는 “산업용 3D프린팅 시장은 독일을 중심으로 유럽이 앞서고 있고 미국도 새로운 기술 시도를 하며 빠르게 성장했다. 세계 시장 구도가 유럽 대 미국이 됐다. 스위스, 이탈리아 등에서도 기술 도입으로 납품시기를 줄이며 경쟁력을 확보하고 있다”고 말했다.
관련기사
- 3D프린팅, 항공우주 분야서 존재감 커졌다2018.04.20
- 우주선 오리온 부품 3D프린터로 만든다2018.04.20
- BMW그룹, 獨 3D프린팅 기술 공장에 1천만 유로 투자2018.04.20
- 센트롤, 위인 피규어 3D프린팅 프로젝트 펀딩 성공2018.04.20
이병국 캐리마 대표는 의료와 패션 분야에서도 3D프린팅 기술이 요긴하게 쓰일 수 있다고 말했다. 신속한 임플란트 생산부터 합리적 가격에 자연스러운 의안, 신속한 패션 아이템 생산 등이 가능하다는 것이다. 3D프린팅 기술과 협동로봇을 결합한다면 대량 생산이 가능하다는 전망도 내놨다.
이 대표는 “장인이 하루에 만들 수 있는 의안은 하나며 가격도 300만원에 달한다”며 “캐리마와 연세대학교가 협력해 개발한 3D프린팅 기술을 이용하면 더 저렴한 가격과 빠른 시간 내 의안을 제작할 수 있다”고 말했다. 이어 “환자 뼈와 똑같은 모양의 뼈를 3D프린터로 뽑아낸 후 수술 전에 의사들이 연습하는 것도 할 수 있다”고 덧붙였다.