우리는 종종 엘리베이터 고장을 경험을 한다. 단순 사고로 탑승자가 지각을 하는 데서 그치기도 하지만, 때로는 중대한 사고로 연결되거나 예측 못한 값비싼 수리 비용을 부담해야 하는 경우도 발생한다. 기업이 비즈니스를 운영하면서 일상적으로 겪는 문제도 크게 다르지 않다. 놀이동산의 인기 있는 신형 놀이기구든, 복잡한 공장의 중요 기계든, 아니면 수익을 창출하는 비즈니스 프로세스든 사소한 사고와 고장이 큰 피해를 가져온다.
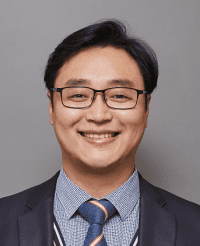
이러한 문제를 해결하기 위해서 많은 기업들이 단편적인 시스템(커스텀이 불가능한 솔루션, 오픈소스 기반 AI 프로젝트 등) 도입을 시도하지만, 일회성으로 멈추거나 사물인터넷(IoT)의 가치를 제대로 경험해 보지도 못하고 시스템 도입을 포기하는 경우가 많다. 그러나 사물인터넷 활용과 더 나아가 데이터 기반의 시스템 운영 방식, 넥스트 로드맵에 대한 전문가들의 가이드나 컨설팅을 받는다면 이야기는 달라진다.
■ 디지털 트윈의 탄생
사물인터넷(IoT) 시대가 오면서 현실 세계에서 일어나는 무수한 움직임을 면밀히 모니터링할 수 있게 됐다. 우리 주변에는 감지 센서가 넘쳐나지만 엣지(edge)와 그 너머로부터 지속적으로 흘러나오는 방대한 데이터를 어떻게 활용해야 할지 아는 기업은 아직 많지 않다.
기업은 데이터를 이용해 비즈니스 신뢰성과 안전성, 투자대비효과(ROI)를 높이고자 한다. 그러나 수많은 정보가 단지 기업의 데이터 레이크를 채우고 클라우드 리소스를 소비하는 고가의 애물단지가 될지, 아니면 결과를 예측·결정하고 흥미로운 기회로 연결 될지는 기업의 데이터 활용도에 달렸다.
여기서 디지털 트윈이 탄생했다. 현실에 존재하는 사물의 정보를 그대로 디지털 세상으로 구현하는 디지털 트윈은 IoT에서 취합할 수 있는 각종 센서 데이터를 통해 현실과 가까운 가상 환경으로 구현하고 다양한 테스트가 가능하다. 기기나 시스템을 정교하게 디지털로 표현해 비즈니스가 의존하는 물리 시스템과 비즈니스 프로세스의 동작을 에뮬레이션, 시뮬레이션, 모델링 및 예측할 수 있고 자동화를 통한 실시간 관리 효율성을 최대화 시켜준다.
디지털 트윈은 생활 속 시스템 에러를 최소화 해준다. 건설업자는 엘리베이터를 최대 용량으로 중단 없이 가동시키는 유지보수 전략을 세울 수 있다. 광산업자는 엄청난 비용이나 생명을 위태롭게 하지 않고도 지면 깊숙한 곳에 위치한 장비의 동작을 평가할 수 있다. 테마파크에서는 전세계 여러 지역에 동일한 신형 놀이기구를 런칭할 수 있으며, 각 지역의 기후에 맞춰 유지보수 기능을 달리 설정해 장애시간을 최소화할 수 있다. 또한, 자동차 제조사가 최적의 생산 능력으로 생산 라인을 가동할 수 있도록 돕는다.
■ 디지털 트윈 운영하기
디지털 트윈 구현은 엘리베이터 규격, 롤러코스터의 브레이크 패드 수 같이 자산을 설명하는 정적인 속성으로 시작한다. 정적 모델은 변수를 평가할 수 있는 기반이 되며, 모니터링 하고자 하는 특성 및 센서 요소를 포함한 데이터는 IT 데이터 저장소에서 통합된다. 즉, 하루에 엘리베이터가 몇 번 멈추는지는 장치의 센서, 카메라 및 다른 서브 시스템에 의해 모니터링 되는 모든 정보로부터 확인 할 수 있다.
그 다음 단계는 가능성을 탐색하고, 니즈를 예측하고, 운영을 최적화하기 위해 산업과 비즈니스 지식을 적용한다. 장치의 시뮬레이션 모델을 만들고, 과거 데이터와 장치가 거치게 될 예상 프로세스를 추가하여 향후 작업을 시뮬레이션 한다.
시뮬레이션 모델이 완성되면, 기업은 여러 가지를 예측할 수 있다. 예컨대 유지보수 주기를 1달에서 2주에 한번으로 단축하면 엘리베이터 시스템의 수명이 3년 더 연장되는 사실을 발견할 수 있다. 이 같은 정보를 은행, 건물, 심지어 비슷한 사양을 가진 건물 복합단지에 있는 전체 엘리베이터를 시뮬레이션 함으로써 더 많은 유의미한 정보를 얻을 수 있다. 물리적 환경을 잘 관리하면서 시간 절약, 고객 경험 개선, 새로운 효율성 발견도 가능하다.
디지털 트윈을 활용해 기업은 각 비즈니스 환경을 자세히 탐색·검토하고, 비즈니스를 최적화하며, 안전과 환경적 책임을 다하는 것은 물론 직원, 고객, 더 나아가 세상을 위한 고차원적 목표를 달성할 수 있다. 디지털 트윈은 보유한 시스템과 그 가능성을 진정 이해할 수 있는 실용적이면서 안전한 툴이다.
■ 제조 현장의 지속적인 개선을 위한 디지털 트윈 기술
디지털 트윈 개념은 제조 산업에서 특히 높은 관심을 끌고 있다. 다양한 유형의 현장 데이터와 결합하여 AI를 적용하고 시뮬레이션과 함께 현장개선에 활용할 수 있다. 디지털 트윈 기술을 적용한 고도화된 산업 분석 모델은 아래와 같이 품질 향상, 이상징후 발견, 공정 최적화 및 강건설계 등 공장 효율성을 향상시킨다.
디지털 트윈을 활용하면 설비 종류, 벤더, 모델, 생산 연도에 상관없이 공장 내 모든 설비를 대상으로 자산 가용성과 성능, 품질을 추적할 수 있다. 예기치 못한 설비 중단, 설비 유휴 상태 지속 및 속도 저하, 거부(설비 시동과 생산) 등 공장 생산성에 영향을 미치는 문제에 즉각 대응할 수 있다.
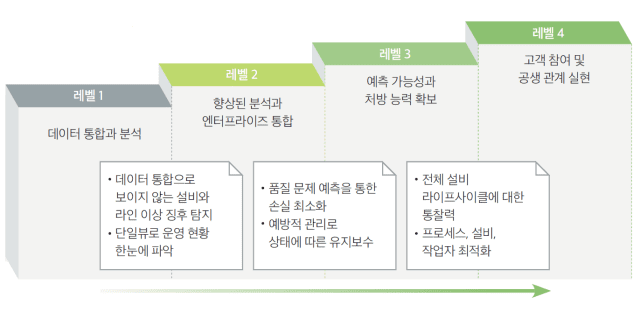
품질 향상을 극대화해 상품 폐기, 재작업, 반품을 최소화하는 등 효율적인 처리도 가능하다. 제조 업체가 이미 운영 중인 품질 시스템에 인사이트가 통합됨으로써 품질 저하 트렌드를 추적해 알림을 보내고, 머신러닝 분석으로 주요 품질 문제를 파악할 수 있다. 생산의 공정 조건 혹은 원료 배치를 기반으로 근본 원인을 파악해 시급한 품질 문제를 예측할 수 있도록 지원한다.
또한, 머신러닝 예측 모델의 모니터링 결과를 실시간 알림으로 제공해 제조사가 성능, 품질, 가용성 관련 이슈에 신속하게 대응할 수 있다. 머신러닝 예측 모델의 모니터링과 알림 시스템으로 파라미터 임계 값 교차 이벤트, 리드 타임과 사이클 타임 예외, 품질 저하 이슈, 이상 징후 등을 탐지해 통보한다. 이상 징후가 발견되면 적시에 찾아내 알려주므로 신속하고 효과적으로 대응할 수 있다.
관련기사
- [기고] 디지털 전환(DX)의 중심, 하이브리드 클라우드2021.02.08
- [기고] 성공적 컨테이너 도입 위한 단계별 핵심 고려사항2021.01.18
- [기고] ‘데이터’ 중심의 디지털 데이터센터 발전 방향2020.12.15
- [기고] 금융 디지털 혁신 앞당기는 AI 기반 ‘데이터 카탈로그’2020.11.25
마지막으로, AI와 머신러닝을 통해 실시간으로 변화하는 공장 조건을 인지하고 원인에 대한 해석을 지원 받음으로써 공정 최적화가 가능하다. AI 해석 모델이 만들어지면 시뮬레이션과 모델 비교를 통해 부품 또는 공차에 대한 품질 표준 또는 기준안 설정이 가능해 설계를 강건하게 할 수 있다. ERP, MES, 실험실 정보 운용시스템(LIMS), 상태감시시스템(CMS), 설비 또는 운영 데이터에 머신러닝 모델을 적용해 변화된 운영 조건을 신속히 공장 현장에 적용하여 작업 전환 시간과 고객 주문 처리에 미치는 영향을 최소화할 수 있다.
효성인포메이션시스템은 ‘루마다 매뉴팩처링 인사이트’를 통해 디지털 혁신 플랫폼을 제공하며 디지털 트윈을 지원한다. ‘루마다 매뉴팩처링 인사이트’는 고도화된 분석 모델을 기반으로 센서 연계, 데이터 통합, 이벤트 알림, 예측, 대시보드 시각화를 아우르며, 디지털 혁신의 모든 단계를 지원하는 제조업 맞춤형 엔드 투 엔드 제품이다. 인텔리전트 매뉴팩처링 성숙도 모델을 기반으로 설계됐으며, 매뉴팩처링 4.0 구현에 필수적인 디지털 혁신 기반을 제공한다. 4M(사람·설비·재료·방법) 산업 분석은 물론 AI와 머신러닝이 탑재돼 설비, 생산, 품질에 대한 통찰력을 제시한다.
*본 칼럼 내용은 본지 편집방향과 다를 수 있습니다.