제조업은 디지털이란 대전환의 격량 한가운데 놓여있다. 좋은 품질의 상품을 생산해 판매하는 업의 본질은 변하지 않았다. 단, 소비자가 제조업에 바라는 것이 '상품'에서 '경험'으로 바뀌었다. 소비자의 요구사항을 즉시 받아들여 실제 제품에 반영하지 못하면, 경험을 바라는 소비자를 놓칠 수 있다.
다쏘시스템은 25일 서울 사옥에서 기자간담회를 열고 미래의 스마트 제조업을 위한 솔루션 전략을 소개했다.
패트릭 미셸 다쏘시스템 델미아 상무는 “단순히 물건을 사는 것에서 물건을 구매함로써 경험을 얻는 시대”라며 “각 소비자가 제품을 사면서 느끼는 다양한 행복을 더 강조하는 시대”라고 말했다.
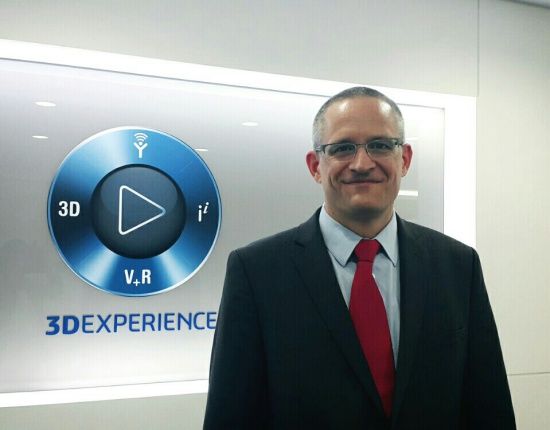
그는 “다쏘는 이런 시대를 맞아 단순히 하나의 공장을 최적화하는 솔루션이 아니라 다양한 각도에서 제조 전반의 최적화를 위한 글로벌 산업 운영 플랫폼을 제안한다”고 강조했다.
다쏘시스템 델미아는 가상의 공장을 지어 프로세스를 시뮬레이션함으로써 실제 공정의 최적화를 돕는 제품이다. 실제로 공장을 짓지 않고 최적의 프로세스를 찾아낼 수 있다.
다쏘시스템은 델미아의 기능을 발전시켜 실제 환경과 가상환경의 연결을 추구했다.
가상과 실제는 디지털로 연결된다. 실제 공장 설비에서 생성되는 수많은 데이터는 미래의 사고를 예측하고, 더 최적화된 공정을 만들어내는데 쓰인다. 분석 결과는 다시 가상환경에 반영돼 더 나은 실제를 만드는 선순환구조를 이룬다.
오늘날 제조현장은 가상환경에서 실제 공장으로 작업지시를 넘기는 단방향 구조로 이뤄져 있다. 가상환경은 새로운 공정을 수립할 때만 생겨났다가 현실로 만들어지는 순간 사라진다.
이런 가운데, 다쏘는 미래의 제조업에 대해 ‘리얼’과 ‘버추얼’을 상존시키는 ‘디지털 트윈(twin)’을 강조하고 있다. 현실에서 벌어지는 일을 데이터로 만들어 분석하고, 그 결과를 즉각 가상환경에 적용해 장단기적인 혁신을 끊임없이 시도하자는 것이다.
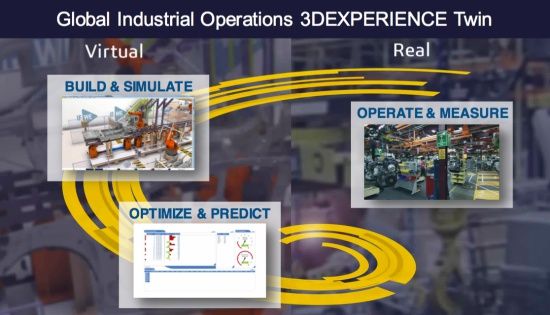
미셸 상무는 “리얼과 버추얼이 각기 따로 가는 게 아니라 세 축이 실시간으로 동시에 유기적으로 결합된 한경을 구축해야 한다”고 설명했다.
이렇게 만들어진 스마트 제조 환경은 시간의 흐름에 따라 ‘최적화-예측-혁신’ 등 3단계의 확산형 순환구조를 갖는다.
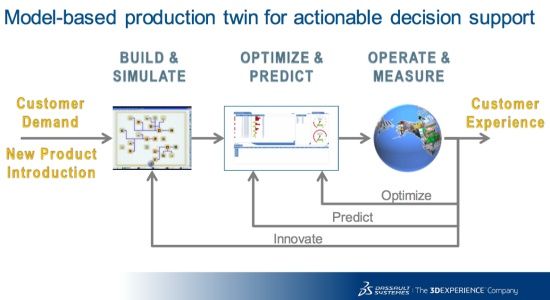
생산 공정 중 매일 일어나는 이슈가 있다. 자재공급이 원활하지 않거나, 설비의 부품이 망가지는 등의 일이다. 설비에 여러 센서 디바이스를 장착해 각 부품의 데이터를 생성할 수 있다. 이 데이터를 모아 패턴을 찾으면 미래를 예측해 공정을 중단시키지 않고 원활한 생산이 가능해진다.
미셸 상무는 “실제 공장에서 발생한 문제를 즉각 인지하고 원인을 찾아 실시간으로 해결할 수 있다”며 “이런 단기 피드백을 해결하는 것이 옵티마이즈(최적화)”라고 말했다.
그는 “단기간 이슈를 해결하다보면, 실제 공장에 데이터가 쌓일 것이고, 이를 통해 기계 고장이나 부품 교체시기를 미리 예측해 대비할 수있다”며 “이같은 중기 피드백이 프리딕트(예측)다”고 덧붙였다.
마지막으로 축적된 정보를 종합해 가상 공장 구축에 활용하면 전반적인 제조공정을 혁신할 수 있다.
그는 “장기적으로 데이터를 통해 패턴을 보면서 새 공급자를 요구하거나 새 프로세스를 만들어야 할 때 전반적인 매뉴팩처링을 현신한다”고 설명했다.
다쏘시스템은 2013년 아프리소(Apriso), 2014년 퀸틱(Quintiq) 등을 차례로 인수하며, 앞서 설명한 글로벌 제조 운영 플랫폼을 구축했다. 디지털 제조, 제조 운영관리, 운영계획 및 공급망 관리 등이 유기적으로 결합됐다. 아프리소는 예측을 가능하게 했고, 퀸틱은 혁신을 뒷받침하고 있다.
패트릭 미셸 상무는 ‘디지털 연속성(digital continuity)’이란 개념을 강조했다. 데이터가 계속 흐르면서 선순환구조를 만들어야 하는데, 여기에 필요한 게 데이터 연속성이란 설명이다. 그는 5가지의 단계로 설명했다.
우선 제품 엔지니어링과 제조 엔지니어링의 연결이다. 설계자가 제품 디자인을 변경할 때 바로 생산기술 측으로 전달돼 빠르게 변화할 수 있게 하는 것이다. 이처럼 설계와 생산기술 간 대화를 가능하게 한 다음은 생산기술과 제조현장의 연결이다. 생산기술로 만든 작업지시서가 종이로 출력되지 않고 곧바로 디지털 데이터 제조 현장에 전달되는 것이다. 로봇 운영 프로그램에도 작업지시서가 바로 전달되는 형태도 가능해진다.
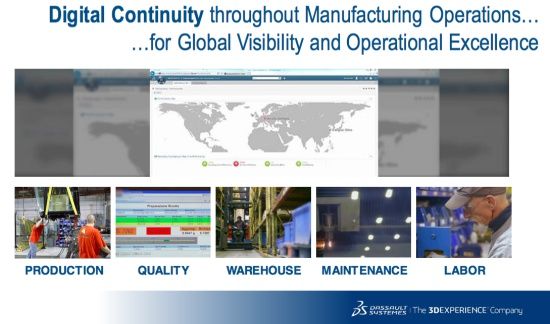
세번째 단계는 ‘설계-생산기술-생산’의 수직적 연속성과 함께, ‘생산-품질-재고-유지보수-근로자’로 이어지는 수평적 연속성이다.
그는 “재고와 생산을 같이 고려하거나, 품질과 생산을 함께 고려함으로써 시간을 절약할 수 있다”며 “현장 인력도 충분한 기술을 갖췄는지 항상 검증해야 한다”고 말했다.
네번째 단계는 글로벌 가시성 확보다. 세계 각 지역별로 흩어진 공장의 생산, 품질, 유지보수 등을 본사에서 명확히 파악할 수 있어야 한다. 그는 “어느 한 곳의 공급지에서 문제가 발생했다고 하면, 공정자체 문제 있을 때 전세계 다른 곳의 공장에 곧바로 반영해 프로세스를 즉각 변경시킬 수 있게 된다”고 설명했다.
관련기사
- 수산중공업, 다쏘 3D익스피리언스 플랫폼 도입2016.05.26
- 다쏘시스템, 대구시에 공인 인증 교육센터 설립2016.05.26
- 다쏘시스템, 포스코에 스마트 공장 시스템 공급2016.05.26
- 다쏘, 프랑스형 '제조업혁신 3.0' 공동 추진2016.05.26
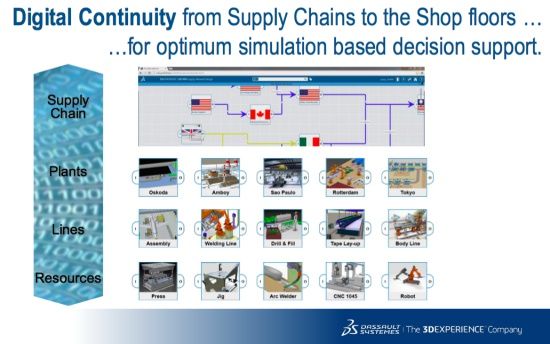
마지막 단계는 글로벌 기업이 리소스, 라인, 플랜트, 서플라이체인 등의 모든 정보를 믿을 수 있는 하나의 데이터로 공유하는 것이다.
그는 “기업이 더 많은 물건을 팔 수 있는 능력을 갖추고, 실제 이윤을 창출하는 프로세스를 갖추는 것이 다쏘시스템의 목표”라고 강조했다.