재활용의 미래가 있다면 이런 모습일까. 페트(PET)병이 공정에 들어가더니 라벨과 이물질을 제거하고 굵은 조각으로 나왔다. 이 조각은 다시 페트병으로 탄생할 수 있는 고품질 소재다. 전체 페트 생산량 중 이런 재활용 소재를 쓰는 경우는 아직 극히 일부다. 이 순환 과정을 확대하려는 세계적인 움직임이 벌어지는 중이다.
수퍼빈이 지난해 경기 화성에 준공한 ‘아이엠팩토리’는 국내 최초 고품질 PET 플레이크 생산 공장이다. 자체 순환자원 회수로봇으로 모은 자원을 13개 공정을 거쳐 플레이크로 만든다. 지디넷코리아는 아이엠팩토리를 찾아 공정에 도입된 기술과 그 의미를 살펴봤다.
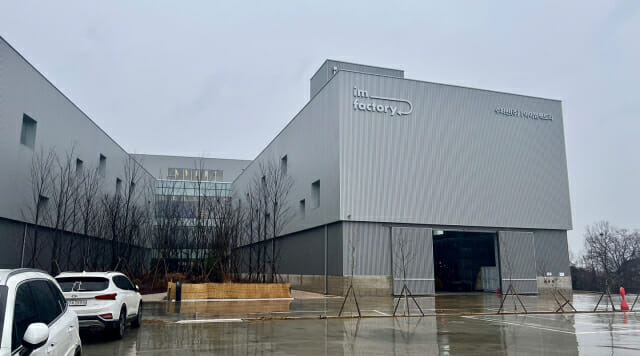
■ "페트 수거해 깨끗한 가루로 만들기까지"
수퍼빈 아이엠팩토리는 1만3천200㎡(약 4천평) 부지에 4천㎡(약 1천200평) 규모로 지난해 준공했다. 이곳에서 연간 1만t에 달하는 플레이크를 생산할 수 있다. 대형 설비를 갖췄음에도 이곳은 다른 공장에서 느껴지는 투박함을 찾을 수 없었다. 세련된 외관과 인테리어와 함께 ‘U자’ 건축물 안쪽에는 작은 숲도 조성했다.
수퍼빈이 회수하는 페트병은 압축된 상태로 입고량을 측정한 뒤 거쳐 공장 본동으로 들어온다. 이곳에서 자원을 투입하면 순서대로 ▲라벨 제거 ▲인공지능 선별 ▲습식분쇄 ▲비중선별 ▲사일로 저장 ▲풍력 선별 ▲온수 세척 ▲세척 및 탈수 ▲건조 ▲물질 및 금속 선별 등 공정을 거쳐 포장된다.
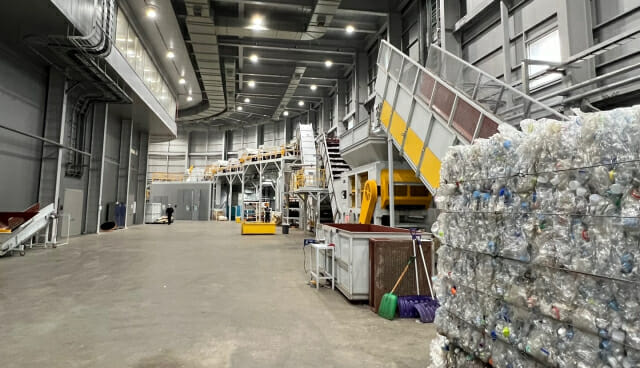
페트병은 먼저 정확한 선별을 위해 낱개로 붙리된 다음 라벨을 제거한다. 인공지능 선별에는 수퍼빈이 보유한 약 2억 장 규모 이미지 데이터가 활용된다. 이곳에서 이물질을 먼저 선별해낸다. 습식분쇄 공정에서는 투명 페트병을 일정 크기 플레이크로 분쇄하고, 이를 비중 선별 공정에서 이물질을 한 차례 더 걸러낸다. 여기까지가 사일로 저장고 앞부분까지의 공정이다.
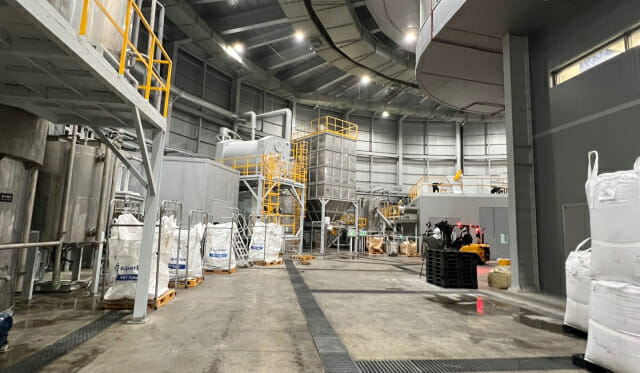
사일로에서 나온 플레이크는 풍력 선별 공정으로 간다. 이곳에서 가벼운 분진이나 라벨을 바람을 이용해 제거한다. 온수세척 공정에서 페트 플레이크에 남아 있는 라벨 접착제 등 이물질을 제거한다. 이를 반복 세척하고 탈수·건조하는 과정을 거친다. 마지막으로 유색 페트나 다른 재질의 플라스틱 등을 최종 선별하면 포장 준비가 끝난다.
본동 2층에는 전체 공정을 한눈에 확인할 수 있는 통합 운영실을 마련했다. 공정 설비에 적용된 센서를 통해 자원 데이터를 확보하며, 자동제어 시스템을 활용해 상태 진단과 정비가 가능하다. 확보된 설비 데이터를 바탕으로 제품 생산 현황 파악과 함께 탄소저감 효과를 확인할 수 있다.
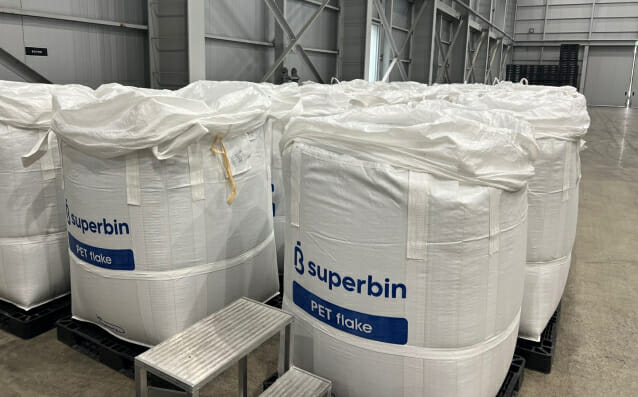
■ "똑똑한 자원 선별 위해 이미지 2억 장 학습"
수퍼빈은 지난 2015년 설립된 이후 인공지능(AI) 순환자원 회수로봇 ‘네프론’을 개발하던 업체다. 이 로봇은 개인이 쓰레기를 거래해 금전적 보상을 얻고, 고품질 쓰레기를 선별 수집해 순환경제 체제를 구축하기 위해 마련했다. 네프론이라는 이름도 ‘혈액을 정화하는 신장 세포 단위’에 따왔다. 세상을 깨끗하게 만들자는 수퍼빈의 구상이 담겼다.
네프론은 재활용 쓰레기를 투입하면 이미지 센싱 AI를 활용해 순환자원 여부를 판단한다. 현재 약 2억 장 규모 이미지 데이터가 라벨링됐고, 딥러닝 방식으로 정확도를 높이고 있다. 자원 형태나 바코드가 훼손되더라도 식별이 가능한 비결이다.
네프론에 라벨이 제거된 음료 투명 페트병을 투입하면 개당 약 10원에 달하는 포인트를 적립해준다. 기기는 현재 전국에 1천45개가 설치됐다. 네프론으로 수거된 자원은 페트 약 3억 개, 캔 약 1억 1천만 개다. 지난달까지 누적 28억 원 규모 환전이 이뤄졌다.
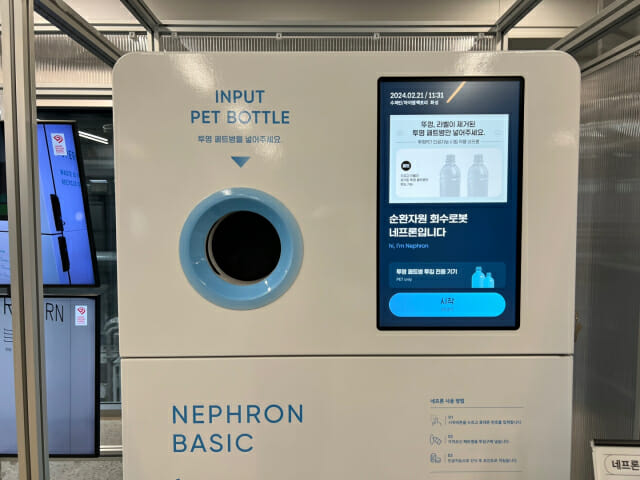
■ "재생원료 확대 필연적…생태계 조성해야"
우리가 흔히 버리는 재활용 쓰레기는 상당 부분이 그대로 소각된다. 혼합배출 시 대량으로 선별하기가 녹록하지 않은 탓이다. 투명 페트(PET)병은 그나마 상황이 나은 편이지만 이마저도 대부분(77%)은 품질이 낮아져 시트나 섬유 등으로 쓰인다.
페트병을 재활용하는 가장 이상적인 방법은 다시 식품용기로 탄생시키는 ‘보틀 투 보틀’이다. 오염이 적은 투명한 페트병을 고품질 재생원료로 만들면 반복 재활용이 가능하다는 의미다. 이를 위해 재생원료 활용률을 끌어올리기 위한 노력이 세계적으로 이어지고 있다.
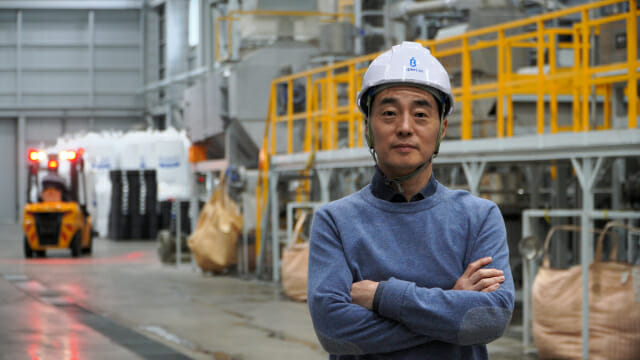
국내에서 이를 식품용기 제조에 사용할 수 있도록 인정된 건 지난해 1월 17일부터다. 식품의약품안전처에 따르면 제도가 마련된 이후 지난 한 해 식품용 투명 폐페트병을 재활용해 만든 물리적 재생 원료 생산량은 약 3천400톤 규모였다. 식품용 페트 전체 생산량의 1% 수준에 불과했다.
관련기사
- 수퍼빈, 삼양패키징에 재생원료 공급 MOU2024.03.23
- 수퍼빈, 파나마시티 자원순환시설 타당성 조사 나서2024.03.14
- 수퍼빈 폐기물공장, iF 디자인 어워드 2개 부문 수상2024.03.07
- 3분기 실적 희비 갈린 네이버·카카오…성장 키워드는 'AI'2024.11.09
한국은 지난해부터 페트 1만 톤 이상 생산 업체에 재생원료 3% 사용 의무를 적용하기로 했다. 오는 2030년까지 플라스틱 페트 생산 시 재생원료를 약 30% 이상 사용하도록 의무화할 계획이다.
김정빈 수퍼빈 대표는 “인간이 만든 모든 제품은 모두 폐기된다”며 “일반 기업들이 재활용 산업 분야에 들어와 스스로 혁신하고 돈을 벌 수 있는 보상과 인센티브 체계가 갖춰질 필요가 있다”고 말했다.