경남 창원에 위치한 LG전자 스마트파크는 국내 가전 업계에서 최초로 세계경제포럼(WEF, World Economy Forum)의 '등대 공장'으로 선정된 스마트공장이다. 또 현재 전세계 유일한 가전 스마트공장이기도 하다.
전세계에 등대공장으로 선정된 공장은 총 103곳이다. 국내에는 LG전자 창원 스마트파크뿐 아니라 포스코 포항 스마트팩토리(2019년), LS일렉트릭 청주 스마트공장(2021년) 등 단 3곳 뿐이다.
LG전자가 지난 6일 창원 스마트파크1를 기자들에게 공개했다. 넓고 쾌적한 작업 환경에 로봇이 어우러진 자동화된 시스템을 직접 보니 공장은 먼지가 날리고 시끄러운 기계음이 울리는 곳이라는 편견이 깨졌다.
* 스마트파크는 보안상 사진 촬영이 불가능해 LG전자 측으로부터 사진을 제공받았다.
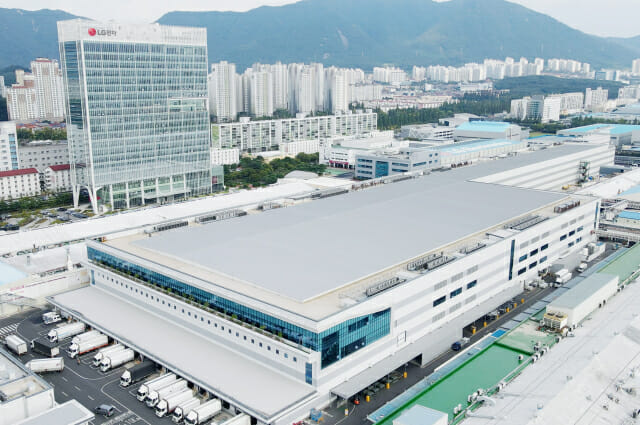
디지털 트윈, AI 기반 자동화 시스템…10분 뒤 상황 예측
LG전자 창원 공장은 1976년 준공돼 46년간 운영되다가 2017년 재건축을 통해 스마트공장으로 탈바꿈했다. 올해부터 '스마트파크'로 명칭을 바꿨다. 공장은 스마트파크1, 스마트파크2, R&D 센터 3곳으로 나뉜다. 스마트파크1의 자동화 시스템은 작년 9월부터 시그니처 냉장고를 시작으로 오브제컬렉션 북미향 프렌치도어, 냉장고 정수기 등 3개 라인을 운영 중이다.
LG스마트파크 통합생산동 1층 로비에 들어서자 오른쪽에 대형 화면이 눈에 띄었다. 화면에서는 '디지털 트윈' 기술로 구현한 현재 가동 중인 생산라인, 부품 이동, 재고 상황, 설비 이상유무, 제품 생산 실적 등을 한눈에 확인할 수 있었다.
디지털 트윈은 디지털 가상공간에 현실과 동일한 대상을 만들고 인공지능(AI)과 빅데이터 등을 활용해 시뮬레이션 함으로써 현실을 분석하고 미래를 예측하는 기술이다.
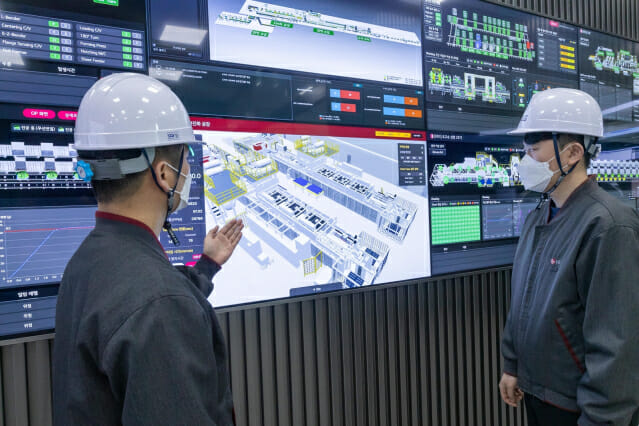
이수형 LG전자 H&A DX/혁신운영팀 선임은 "디지털 트윈은 30초마다 공장 안의 데이터를 수집·분석해 10분 뒤 생산라인의 상황을 예측해 준다"라며 "작업 공정에서 발생할 수 있는 이상 상태에 미리 대비해 업무 효율을 높일 수 있다"고 설명했다.
예를 들어 10분 뒤에 라인 일부에서 자재가 부족해 정체가 될 예정이면, 미리 해결하도록 안내해 사고를 막을 수 있다. 또 실시간으로 생산 과정을 시뮬레이션 하기 때문에 한 개 라인에서 여러 종류의 제품을 생산하는 공정에 맞춰 부품과 자재를 적시에 공급하는 것이 가능하다. 기존 시스템에서는 작업자가 자재가 부족하다는 것을 일일이 파악하고, 요청했기 때문에 시간이 더 오래 걸렸다고 한다.
이수형 선임은 "디지털 트윈 기술로 예기치 못한 설비 고장으로 작업이 중단되는 시간이 96% 감소하고, 재료 손실도 80% 절감할 수 있게 됐다"고 말했다.
디지털 트윈 시스템에서 사용되는 데이터량도 막대하다. LG전자는 공장 곳곳에 센서를 설치해 생산과정 전반에서 데이터를 수집하고 있다. LG스마트파크 통합생산동에서 하루에 수집하는 데이터량은 약 500GB다. 기존 냉장고 생산라인의 일 평균 데이터 수집량인 50MB 대비 1만배 가량 많은 수치다.
물류로봇, 고공 컨베이어가 컨테이너 옮기는 '입체물류 자동화'
3층으로 이동해 본격적으로 스마트공장 내부를 둘러봤다. 가장 먼저 드는 생각은 '쾌적하다'였다. 공장에서는 사람들이 부품을 들고 이동하는 모습을 볼 수 없었다. 그 대신 여러 대의 물류로봇(AGV, Automated Guided Vehicles)들이 자재를 옮기고 있었다. 현재 창원 스마트파크에는 3가지 종류의 물류로봇(AGV) 50대가 운영되고 있다.
스마트파크 바닥에는 녹색, 노랑색 라인들이 줄지어 있었다. 녹색 라인은 로봇이 이동는 경로, 노랑색 라인은 사람이 지나가는 통로다. 물류로봇은 바닥의 녹색 라인 마다 부착된 QR코드 인식을 통해 경로를 파악하고 움직인다. QR이 훼손되면 로봇은 멈추고 알람을 보내기 때문에 유지보수가 가능하다. 물류로봇은 LG유플러스가 구축한 5G 전용 통신망을 통해 움직인다.
이날 투어 도중 여러 명이 통로를 막는 상황이 벌어지자, 물류로봇은 경로에서 이동해 달라는 알람을 울렸다. 로봇에 부착된 센서가 사람, 장애물들을 인식한다는 것을 알 수 있었다.
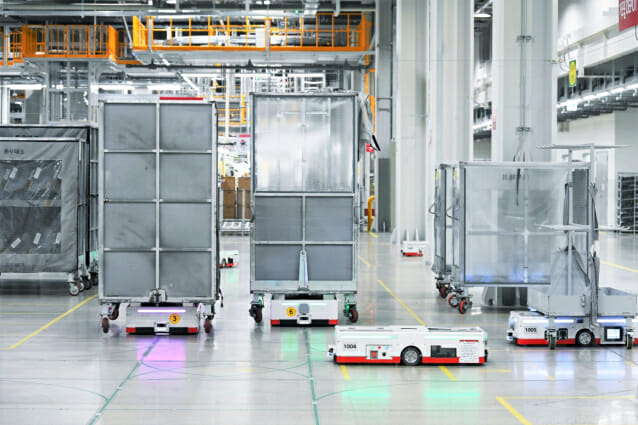
이수형 선임은 "기존에는 트럭에서 자재를 지계차를 사용해서 옮기는 수작업 기반이었고, 자재 이동을 제때하지 못해 불량이 생기는 경우가 많았다"라며 "스마트공장은 화물차 높이와 동일한 높이의 도크를 만들어서 직납 입고 방식을 구축했고, 물류 엘리베이터를 이용해 25초 간격으로 600kg 부품 박스를 3층으로 빠르게 옮긴다"라고 설명했다.
그 다음 물류로봇(AGV)이 컨테이너를 지능형 무인창고로 옮기고, 고공 컨베이어가 천장에서 최대 30kg의 박스를 옮겨준다.
입체물류 자동화 시스템 도입으로 자재 공급시간은 기존 대비 25% 단축됐고, 물류면적은 30% 정도 감소했다. 예기치 못한 설비 고장으로 작업이 중단되는 시간도 96% 감소했다. 전체 생산라인은 총 470미터로 이전 보다 단축됐다.
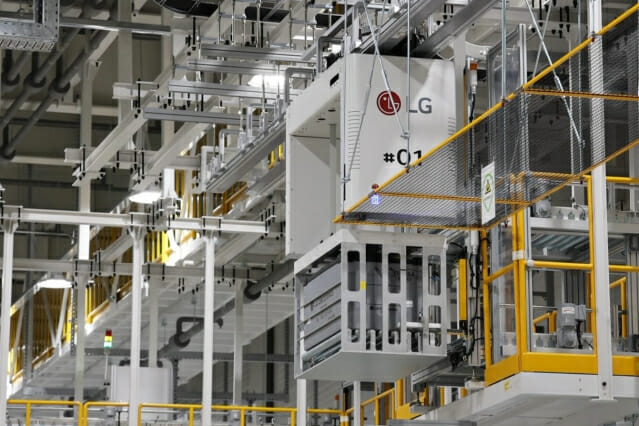
로봇팔이 20kg 무게의 냉장고 문 조립…생산량 20%↑ 불량률 30%↓
창원 스마트공장의 특징은 1개 생산라인에서 다양한 냉장고 모델을 제조할 수 있다. 즉, 다품종 소량 생산이 가능하다는 애기다. 현재 1개 라인에서는 최대 58종의 냉장고모델을 생산한다. 컨테이너에서 작업 중인 냉장고의 색상을 살펴보니, 제각기 다른 색상이었다. 이 또한 디지털 트윈 기술 덕분에 가능한 시스템이다.
생산라인에 들어서자 분주하게 움직이는 로봇팔이 보였다. 로봇팔은 20kg이 넘는 커다란 냉장고 문을 들어 본체에 조립한다. LG전자는 로봇팔에 자체 개발한 3D 비전 알고리즘을 적용해 로봇이 정확한 작업을 할 수 있도록 만들었다.
강명석 LG전자 키친어플라이언스생산선진화Task 리더는 "예전에는 사람이 냉장고 문을 부착하는 작업을 직접했을 때, 속도가 일정하지 않았다"라며 "숙련된 작업자도 오전에는 컨디션이 좋아 작업속도가 빠르다가 오후가 되면 피로가 누적돼 속도가 느려지곤 했다"고 말했다. 이어 "냉장고 문 부착 작업을 사람이 했을 때 평균 속도가 15초였다면, 자동화 도입 후 13초 이하의 일원화된 속도를 유지할 수 있게 됐다"며 "균등한 품질이 기능해졌고, 시간당 제품 생산대수는 20% 가까이 증가했다"고 밝혔다.
또 기존에는 용접 시 가스산화물이 발생됐지만, 이를 전자유도방식 신공법으로 바꿔 안정성을 높였다.
다음 단계인 PCB 공정에서는 사람이 직접 제품을 조립하고 있었다. 리드와이어, 하네스 등 가는 선들은 로봇이 집기 어렵기 때문이다.
완성된 냉장고는 성능 검사를 하기 위해 물류 엘리베이터를 통해서 4층으로 이동된다. 총 2시간에 걸쳐 4가지 성능 검사를 하고, 최종 합격한 냉장고는 다시 3층으로 내려와 무인 포장 시스템을 통해 포장된다.
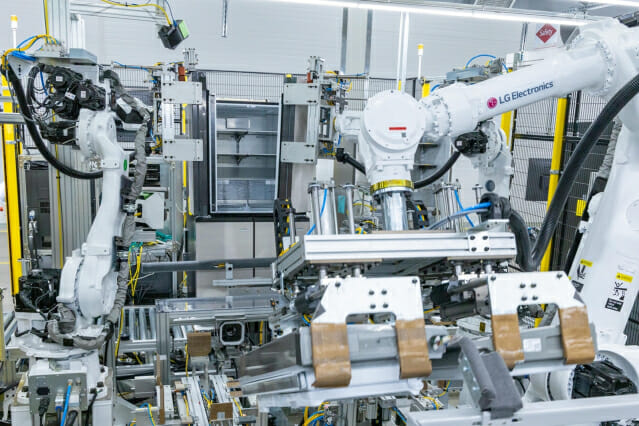
2025년 최종 완공…글로벌 사업장에도 '지능형 자율 공장' 도입
창원 스마트파크는 현재 자동화율이 65%이며, 2025년 최종 완공될 예정이다. 냉장고 생산라인 1개를 추가하고 오븐, 식기세척기 라인도 확대 구축하게 된다. 또 LG전자는 글로벌 생산거점에도 단계적으로 '지능형 자율 공장'을 도입할 계획이다.
관련기사
- LG전자, 수익성 악화에도 연간 영업이익 4조원 첫 돌파 전망2022.10.07
- LG전자, 3분기 매출 분기 최대…영업이익은 기대치 밑돌아2022.10.07
- 이상규 LG전자 사장, 금탑산업훈장 수상2022.10.05
- LG전자, 아프리카서 '올레드 TV 포장 박스'로 만든 예술 작품 전시2022.10.04
강명석 리더는 "많은 사람들이 스마트공장으로 바꾸면서 기존 인력을 감축했을 것으로 추측하는데, LG스마트파크에서 근무하는 직원 수는 스마트공장 구축 전과 비슷한 수준"이라며 "주로 위험하고 까다로운 작업을 로봇이 맡고 작업자는 생산라인이나 로봇을 모니터링하고 관리하는 업무를 맡아 생산성과 품질을 향상시켰다. 결국 사람을 위한 자동화라고 봐야 된다"고 강조했다.
그는 이어 "LG전자가 창원 사업장의 생산성을 꾸준히 향상시키고 생활가전 사업에서 지속적인 성과를 창출하면서 부품을 공급하는 11개의 주요 협력사의 종업원 수는 지난해 말 기준 4천700여명으로 스마트파크 가동 전인 2020년 말 대비 약 15% 늘었다"고 말했다.