저온에서도 양질의 전고체전지 전해질을 만들어 극판과 멤브레인 분리막에 적용하는 기술이 개발됐다.
한국전기연구원(KERI, 원장 직무대행 김남균)은 차세대전지연구센터 하윤철 박사팀이 '저온 소결형 고체 전해질 분말 제조 및 시트화 기술'을 개발, 이차전지 전문기업에 이전했다고 18일 밝혔다.
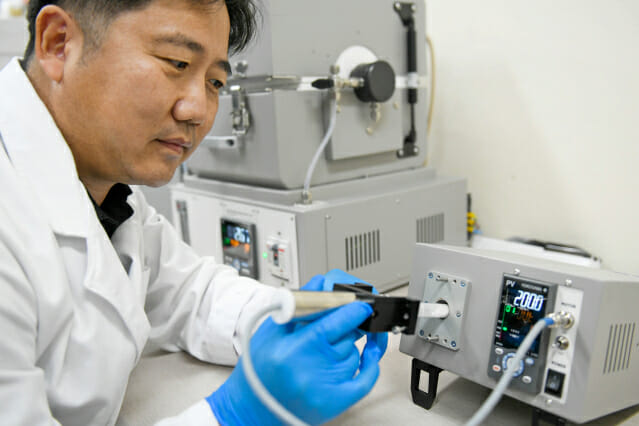
전고체전지는 양극과 음극 사이에서 이온을 전달하는 전해질을 액체가 아닌 고체로 대체한 차세대 배터리다. 화재 위험이 없고 용량이 큰데다, 사용 목적에 따라 다양한 형태로 제작할 수 있다.
전고체전지는 전해질이 고체라 전극이나 분리막을 만드는 단계에서 다른 물질과의 계면 접촉이 중요하다. 고체 전해질은 보통 500℃ 이상 고온에서 만드는데, 바인더 등 다른 전지 소재는 열에 약하다는 문제가 있다.
고체 전해질을 바인더나 도전재, 활물질 등 다른 소재와 혼합하려면 미세한 입자로 분쇄해야 해 이온 전도도가 낮아진다. 혼합 후에도 소결 등 열처리에 제약이 있어 계면이 잘 안 만들어지는 문제가 발생한다. 온도를 높이면 소재가 손상되고, 온도를 낮추면 품질이 떨어지는 상황이 벌어진다.
하윤철 박사팀은 자체 개발한 '중간재 활용 습식 밀링 공정'을 기반으로, 200℃ 이하의 결정화 온도에도 500℃ 이상에서 열처리한 기존 방식과 대등한 수준의 이온 전도성을 갖는 고체 전해질 제조 기술을 개발했다.
열처리 온도를 200℃ 이하로 낮춤으로써 고체 전해질을 바인더와 도전재 등 다른 소재와 섞어 시트로 만들어 전극을 제조하고 한번에 열처리해 마무리할 수 있게 됐다. 기존 고온 열처리 방식을 쓰면 이 과정에서 계면 저항이 크게 발생하는 문제가 있었다.
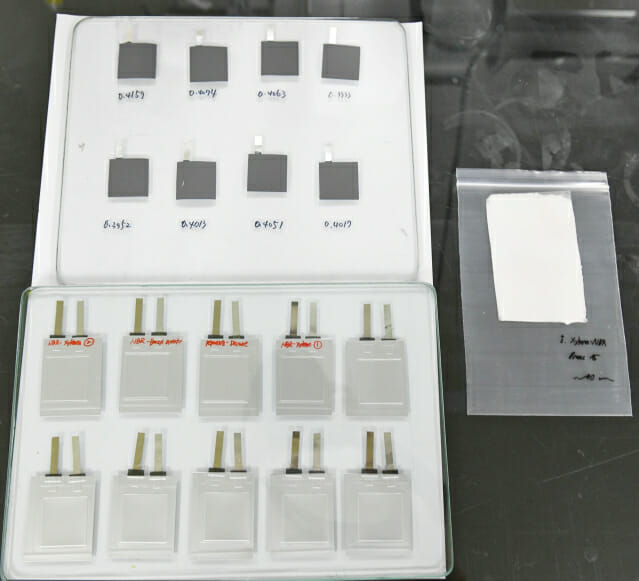
이러한 습식 밀링 공정과 저온 소결 방식을 쓰면 전극 제조나 멤브레인 제조 등 활용 목적에 따라 고체 전해질의 크기를 알맞게 제어·조절할 수 있고, 고체 물질 간 계면 저항도 낮춰준다. 제조 공정에서 에너지 비용도 줄일 수 있다.
관련기사
- 정부, 차세대 전지 초격차 R&D 전략 9월까지 수립2022.06.10
- LG엔솔, 차세대배터리 공동연구 나선다2022.06.07
- 수명 긴 배터리 만들 때 좋은 소재만큼 중요한 것은?2022.05.02
- 전기연, 차세대 리튬황배터리 수명 연장 기술 개발2022.04.11
이차전지 장비 전문기업 하나기술(대표 오태봉)은 최근 이 기술을 이전받았다. 전고체전지용 고체 전해질 시트 제조설비와 시트용 고체 전해질 소재 양산 기술을 2023년 말까지 확보할 계획이다.
하윤철 박사는 "고체 전해질의 이온 전도도 향상이나 대량생산에 머물렀던 관점을 넘어, 전극 혹은 멤브레인 공정까지 고려했다는 측면에서 완성도와 실용성이 높은 성과"라며 "전력저장장치(ESS)나 전기차 등 분야 전고체전지 상용화를 위한 소재·극판·셀 공정기술 개발을 위해 노력할 것"이라고 말했다.