“신뢰성이 보증되지 않으면 절대 출시하지 말라는 게 저희 CEO의 방침입니다.”
지난달 31일 경상남도 창원시 LG전자 창원 2공장에 들어서자 조성화 LG전자 세탁기개발품질보증팀 차장이 이같이 강조했다. ‘의류가전의 메카’라고도 불리는 이 곳은 1987년 가동을 시작해 현재 트윈워시, 건조기, 스타일러, 통돌이 세탁기 등 LG전자 의류관리 가전 전 제품을 생산하고 있다.
면적은 52만6천 제곱미터로 처음 구축된 30년 전 대비 생산성은 10배 가까이 확대됐다. 그동안 축적된 노하우로 공정 자동화를 통해 생산성을 높여 수요에 대응하고 있으며 인간의 심장에 비유되는 컴프레서, 모터 등 핵심 부품들도 모두 이 곳에서 탄생됐다. 특히 내구성 강화를 위해 혹독한 제품 테스트를 거쳐 신뢰성 확보에 나서고 있다.
소비자의 니즈가 세탁뿐 아니라 건조, 의류관리까지 이어지면서 세탁기, 건조기 등 의류관리 가전 산업이 빠른 속도로 성장하고 있다. 이 때문에 창원 공장의 의류관리 가전 생산라인은 지난 1월부터 예년보다 빠르게 가동을 시작해 트윈워시와 건조기가 지난해 같은 기간 대비 각각 20%, 30%, 스타일러는 150% 이상 늘었다.
1969년 국내 최초 세탁기를 선보인 LG전자는 살균, 편의, 옷감 유지를 위한 세탁기와 가옥구조 변화, 미세먼지 등 대기질 오염 등 환경 트렌드를 반영한 건조기, 착용 니즈를 반영한 트롬 스타일러까지 선보이며 세탁 문화을 이끌어왔다.
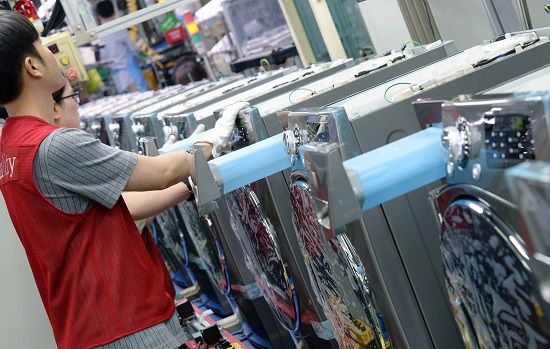
■끊임없는 자동공정화…생산 속도·품질·원가 경쟁력↑
창원 2공장에 들어서자 ‘위잉’하는 소음이 가득하다. 무인 로봇 등 자동화 장비들이 제품을 나르고 확인하고 포장하는 작업이 진행되는 소리다. 회사는 매년 수요가 늘 것에 대비해 최근 2년간 생산 효율화를 위한 자동화 설비 투자에 역량을 집중해 왔다. 트윈워시, 건조기, 스타일러 등 의류관리 가전의 제조라인 자동화율은 60%대에 달한다.
정나라 리빙어플라이언스제조팀 차장은 “중량물이 8kg가 넘는 제품을 하루 2천~3천개씩 옮기는 작업자들의 질병 유발과 생산성 향상을 위해 현장에서 일하는 작업자들의 아이디어를 반영해 실제 필요한 생산라인에 적용했다”며 “지난해보다 라인당 5명씩 더 뽑아 인력 고용 문제를 해결하고 늘어나는 수요에 대한 대응력도 높여가고 있다”고 설명했다.
제조라인 입구에는 세탁기와 건조기의 몸체인 ‘캐비닛(Cabinet)’을 접는 자동화 장비가 있다. 이 설비는 평면으로 펼쳐져 있는 스테인리스 캐비넷을 1초도 안 돼 ‘ㄷ’자 모양으로 한 번에 접는다. 공장 안쪽으로 조금 더 들어가자 무인차가 지나다니며 부품 등 물류를 라인에 직접 공급하는 모습이 보인다. 이 곳에서 생산되는 의류관리 가전은 기본적으로 모두 11초에 한 대씩 생산된다.
이 같은 생산 속도를 맞추기 위해서는 자동화가 필수다. 생산 공간 확보와 작업자의 움직임을 최소화하기 위해 자동 운반 설비들이 제조라인을 따라 작업자들의 머리 위로 움직인다. 약 20미터 길이의 트롤리(Trolley)는 무겁고 부피가 큰 세탁조를 보내고 작업자 옆 부품 자동 공급 설비(SPS)가 도어, 상판 등 제품 조립에 필요한 부품을 작업자 손 근처로 옮겨준다.
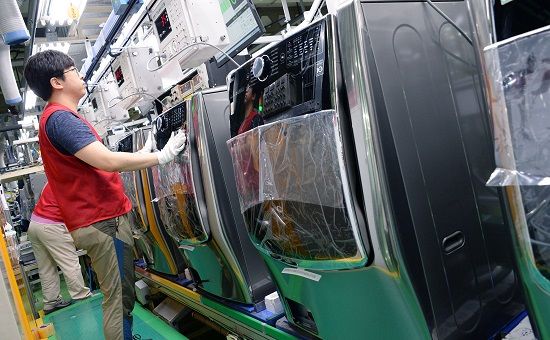
장 차장은 “SPS 역시 작업자들의 아이디어를 반영해 설치하게 된 설비로 공정 개선에 큰 도움이 됐다”며 “이전처럼 허리를 굽히지 않고도 작업할 수 있게 됐으며 라인 밸런스를 맞추는 조건에서 건조기는 11초, 탑로딩 제품은 9초에 한 대씩 생산하며 기존보다 생산성이 30% 이상 개선됐다”고 말했다.
조립 공정이 끝나면 품질 검사가 시작된다. 작업자들이 세탁통 내부에 물을 채워 헹굼, 탈수 등이 제대로 작동하는지 품질 기준에 따라 검사한다. 품질 검사를 통과한 제품만 포장 공정으로 넘어갈 수 있다. 마지막 포장 공정에서는 자동화 설비가 제품을 자동으로 포장한다. 자동점검 시스템은 포장박스 안 액세서리, 부품들까지 제대로 들어갔는지 신속하게 확인한다.
생산 효율성은 LG전자의 모듈러 디자인을 통해서도 이뤄진다. 이는 여러 부품을 통합, 표준화해 레고 블록처럼 독립된 패키지로 만들어 다양한 모델에 사용 가능하도록 한다. 회사는 2005년 가전 제품에 이 디자인을 도입해 3~4개 모듈만으로 세탁기, 건조기 등을 제조하고 있다. 모터, 컴프레서 등 모듈화된 부품은 이 곳에서 생산하거나 협력사에서 공급받는다.
이에 제조라인 입구부터 컨테이너에 실리는 순간까지 채 15분을 넘지 않는다. 컨테이너에 실린 제품은 국내 판매 물량은 전국의 물류 창고로, 수출용은 부산항으로 각각 배송된다. 생산라인 관계자는 "창원 2공장은 설립된 직후 연간 50만대 규모로 생산했지만 현재 자동 공정화 등 노력으로 A1동 리빙어플라이언스 공장을 면적을 넓히지 않고도 생산량을 500만대까지 확대했다"고 전했다.
■“돌리고, 얼리고” 24시간 혹독한 신뢰성 테스트
"쾅- 쾅- 쿵- 쿵-"
세탁기, 건조기, 스타일러 등 LG 의류관리 가전의 신뢰성은 A1동 생산라인 뒤쪽의 신뢰성 시험동에서 혹독한 검증을 거친다. 처음 들어가자 보이는 것은 도어 개폐 실험실이다. 자동화 테스트 장비가 제품의 문을 1만회 이상 반복적으로 열고 닫는 극한 테스트가 진행 중이었다. 미니워시 도어는 자동 서랍 개폐기를 이용해 문이 강하게 끊임없이 여닫힌다.
신뢰성 시험동 1층에서는 세제 투입 시험 등이, 2층에서는 상온고온저온의 온도 시험, 과진동 시험, 도어 개폐 시험 등이 이뤄진다. 개폐실을 지나자 '고온 Room', '저온 Room' 팻말이 보인다. 상온, 열대 기후의 고온이나 극지방 영하의 저온에서 10년 이상 사용해도 품질에 변화가 없는지 시험한다.
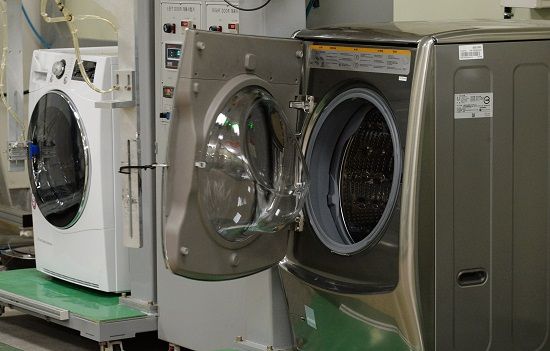
고온실에 들어가자마자 물기가 피부에 송골송골 맺힐 정도의 습기와 숨을 턱 가로막는 후덥지근한 열기가 느껴졌다. 세탁기, 건조기 등 제품이 나란히 놓여 테스트를 견뎌내고 있다. 정 차장은 "2층 건물인 신뢰성 시험동은 500대 이상의 제품을 동시에 시험할 수 있다"며 "각 제품 테스트 기간은 보통 3달에서 길게는 반년 이상까지도 소요된다"고 설명했다.
진동 실험실에서는 제품들이 특정 조건에서 발생할 수 있는 과도한 진동을 견뎌낼 수 있는지 시험한다. 모든 가능성을 확인하기 위해 최소 30여 종류의 옷감을 중량을 달리해 시험한다. 또 두꺼운 고무, 모래포대 등 실제 사용하는 의류보다 훨씬 무거운 소재를 넣어도 제품이 손상 없이 정상적으로 작동하는지 검사한다.
관련기사
- 건조기 수요 급증…LG·린나이·삼성 경쟁 치열2017.06.01
- 열 안쓰고도 30분 만에 빨래 말리는 건조기 '화제'2017.06.01
- LG 드럼세탁기, 유럽서 연이어 최고 평가2017.06.01
- LG전자, 美 테네시주에 세탁기 공장 짓는다2017.06.01
특히 두 개 세탁기를 결합한 트윈워시는 상단 드럼세탁기와 하단 미니워시를 동시에 탈수하는 경우에도 이상이 없는지 확인하는 것은 매우 중요하다. 탈수 단계에서 제품 진동이 가장 크게 발생하기 때문이다. 탈수 단계에서 세탁조가 회전하는 최고 속도는 상단 드럼세탁기가 1천10rpm(분당 회전수), 하단 미니워시가 700rpm에 달한다.
각 테스트의 전압도 다르게 적용된다. 정 차장은 "글로벌 생산기지는 11곳이며 우리나라의 경우 프리미엄 제품을 생산해 수출하고 있다"며 "각 국가별로 사용하는 전압이 다르기 때문에 각 환경에 맞는 테스트를 진행하는 것"이라고 설명했다.