제조업에서 결함 여부를 판단하기 위한 품질검사는 필수 공정이다. 하지만 주로 작업자의 경험이나 육안에 의존하고 있다. 제조업의 디지털 제조가 가속화하면서 이런 결함검사를 지능화하는 기술 개발이 요구되고 있다. 다양하고 복잡한 형상에 공통적으로 적용할 수 있는 자동검사 시스템 개발은 스마트팩토리 솔루션의 핵심 기술로 꼽힌다.
한국생산기술연구원(원장 이상목, 이하 생기원)은 인공지능(AI) 기술을 활용한 ‘결함검사 플랫폼 기술’을 개발하고, 이를 바탕으로 의료용 카테터의 복잡한 형상을 자동 검사할 수 있는 시스템을 개발했다고 31일 밝혔다.
생기원 AI응용설비연구센터 윤종필 수석연구원은 머신비전을 이용한 기존의 결함검사 방식에 AI기술을 접목, 딥러닝 알고리즘을 통해 불량 유무를 정확하게 측정·판단할 수 있는 결함검사 플랫폼 기술을 개발했다. 또 바이오메디컬센터 최동윤 수석연구원은 이 개발 성과를 의료용 카테터에 적용해 복잡한 내부구조 때문에 자동화가 어려웠던 카테터 튜브 단면의 형상 결함을 자동 검사할 수 있는 시스템을 개발했다. 생기원은 이 시스템이 "세계 최초"라고 강조했다.
의료용 카테터는 약물 주입, 혈액 배액 등 치료 및 진단기기 역할을 하는 튜브로, 체내에 삽입하는 제품의 특성상 형상 및 치수의 품질 관리가 중요하다. 다품종 소량생산 품목이면서 약물이나 혈액이 이동하는 통로인 내강(Lumen) 개수와 형상도 다양한데, 특히 다중 내강(Multi-lumen) 카테터의 경우 결함 종류가 다양하고 형태도 일정치 않아 검사 자동화가 어려운 분야로 꼽혀 왔다.
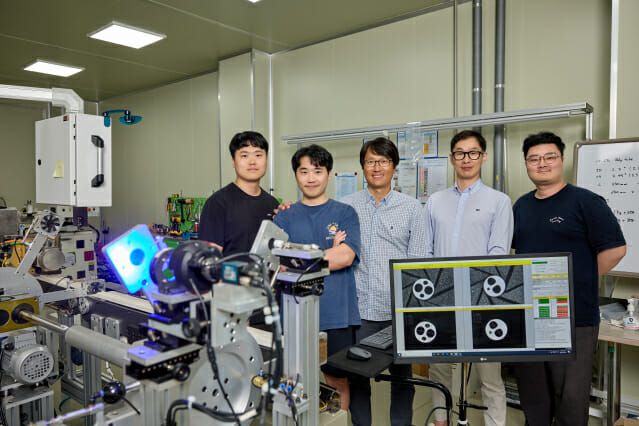
연구팀은 카테터 튜브의 정확한 단면 이미지를 촬영할 수 있는 머신비전 시스템을 개발하고, 딥러닝의 CNN(Convolutional Neural Networks, 이미지나 영상 데이터 처리에 쓰이는 알고리즘) 구조와 트랜스포머(Transformer, 구글이 개발한 AI 알고리즘)의 어텐션 메커니즘을 응용해 제품의 구조적 특징을 반영할 수 있는 결함 검사 알고리즘을 개발했다. 이 결과를 당초 설계한 형상 수치와 실시간 비교하며 제품 등급과 불량 여부를 자동 판단하는 시스템을 구현했고, 딥러닝 기술로 단면의 중심축 회전에 상관없이 튜브 단면의 복잡한 형상도 정확하게 검사할 수 있게 됐다고 생기원은 설명했다.
이를 통해 마이크로미터 수준 카테터 형상의 결함을 판정할 수 있는 기술을 확보하고, 육안 검사 시 최대 5분 정도 소요되던 검사 시간을 3∼5초로 단축했다. 특히 데이터 기반(Data-driven) 방식과 규칙 기반(Rule-based) 방식의 장점을 결합한 하이브리드 방식을 채택해 검사 기준이 변경돼도 재학습할 필요가 없다.
기존 AI기반 결함검사 기술은 정상 및 불량 제품의 데이터를 학습해 불량 유무를 판단하는데, 작업 환경이나 기준 수치가 바뀔 때마다 다시 데이터를 수집하고 재학습하는 번거로운 과정을 거쳐야 한다. 연구팀은 데이터 드리븐 방식의 딥러닝을 활용해 AI가 카테터 단면 이미지에서 특정 지점들(Key points)의 위치를 스스로 찾고 측정할 수 있도록 설계했다. 또한 규칙 기반 방식을 적용, 획득한 측정값을 다양하게 조합해 재학습 없이도 정상 및 불량 제품을 평균 95% 정확도로 판단했다.